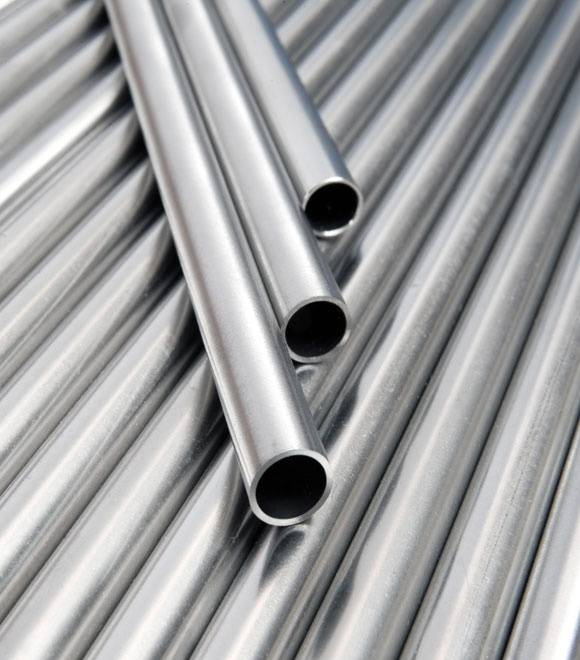
Regular size:
Thickness:≥0.5mm
Outer diameter:≤214mm
Length:≤6000mm
The titanium tube is light in weight, high in strength and superior in mechanical properties. It is widely used in heat exchange equipment such as tubular heat exchangers, coil heat exchangers, serpentine heat exchangers, condensers, evaporators and pipelines. Many nuclear power industries use titanium tubes as their standard units.
Different grades for different purposes
There are many different grades of titanium, and they all have various characteristics that make them ideal for specific sectors of the chemical process industry. Titanium grades 1, 2, 7, 9, and 12 have been used in the past for high-quality, corrosion-resistant heat transfer equipment.
The most commonly-used grades of titanium for heat transfer equipment are grade 2, unalloyed (commercially pure) titanium are grade 7, and basic grade 2 with a palladium addition for increased corrosion resistance. Grade 1 is used primarily for plate and frame exchangers, while grade 9 (with aluminum and vanadium additions) is used for shell and tube exchangers when higher strength is required for the tubing. Grade 12 is an alloy of titanium with a small amount of molybdenum and nickel and is used for slightly high strength and higher corrosion resistance, especially where crevice or under-deposit corrosion may be an issue.
Titanium tubes can be used in applications where the fluid in the tubes move at high velocities and are normally used with a zero-corrosion limit, thus reducing the required wall thickness. Titanium is resistant to fouling, has a high corrosion fatigue limit, and is resistant to impingement or erosion attack. Therefore, titanium is ideally suited for a wide variety of heat transfer applications – especially those involving seawater, brackish water cooling, or steam heating. When the corrosivity of the chemicals make it necessary to use higher alloys like titanium, it is essential that the system be designed for maximum efficiency to ensure that the overall cost of the heat transfer is minimized. This will stand true regardless of the design used for the heat exchanger.